Технология. Рубрика в журнале - Вестник Южно-Уральского государственного университета. Серия: Машиностроение
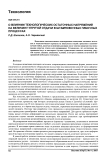
Статья научная
Выполнено математическое моделирование поведения листовых заготовок в технологическом процессе из нескольких стадий: прокатки и штамповочной гибки, включая изменение размеров после снятия нагрузки (так называемая упругая отдача или пружинение). Установлено, что остаточные напряжения могут в некоторых случаях существенно изменять величину упругой отдачи; указаны диапазоны условий, в которых влияние остаточных напряжений необходимо учитывать.
Бесплатно

Статья научная
Рассмотрены вопросы обеспечения точности базирования сменных узлов автоматизированных производств, на основе анализа размерных цепей, возникающих при обработке базирующих отверстий сменного узла. Рассмотрены вопросы обеспечения точности обработки деталей с применением автоматически сменных узлов на рабочей позиции перекомпонуемых производственных систем (RMS). Показано суммирующее влияние точности базирования автоматически сменных узлов на точность многосторонней обработки деталей. Для решения вопросов многосторонней обработки деталей рассмотрена модель автоматически сменного узла - носителя деталей, для моделирования вопросов обеспечения точности базирования носителя на рабочей позиции перекомпонуемой производственной системы. Приведена конструкция носителя, выполненного в виде правильной прямоугольной призмы, где на боковых гранях расположены базирующие отверстия, а установку комплекта приспособления и детали выполняют в плоскости каждой грани. При этом обеспечивается пространственная повторяемость положения деталей относительно технологических узлов рабочей позиции, и равная жесткость корпуса носителя в направлениях многосторонней обработки деталей. В статье рассмотрена модель системы равнорасположенных базирующих отверстий для моделирования точности базирования носителя. На основе размерного анализа показано влияние взаимного расположения каждого базирующего отверстия носителя на точность обработки детали. Данный аспект является определяющим для реализации многосторонней обработки деталей на носителе. Показано, что на точность многосторонней обработки деталей оказывают влияние вариантность размерных цепей обработки базирующих отверстий. Проведен анализ вариантных размерных цепей обработки базирующий отверстий носителя. Приведены условия необходимые для обеспечения точности базирования носителя при многосторонней обработке деталей и методика расчета параметров обработки базирующих отверстий. Таким образом, совместное рассмотрение представленных аспектов обеспечения точности обработки базирующих отверстий позволит решить задачи обеспечения точности многосторонней обработке деталей с применением автоматически сменных узлов на рабочей позиции перекомпонуемых производственных систем.
Бесплатно
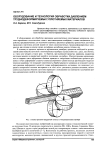
Оборудование и технология обработки давлением труднодеформируемых уплотняемых материалов
Статья научная
Приведен обзор способов и устройств, применяемых для обработки давлением труднодеформируемых материалов. Описаны особенности прокатки таких материалов с многосторонним обжатием
Бесплатно
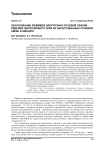
Статья научная
Рассмотрены вопросы выбора оптимальных режимов электронно-лучевой сварки нагартованных алюминиевых сплавов типа АМг6Н и АМг6НПП с различной степенью упрочнения (15, 30 %). Цель оптимизации режимов - обеспечить наименьшую степень разупрочнения и размеры разупрочненных зон в диапазоне значений, гарантирующих равнопрочность сварных соединений основному металлу оболочковых конструкций. Приведены особенности изготовления цилиндрических изделий из алюминиевых нагартованных сплавов с применением электронно-лучевой сварки. Для уменьшения размеров разупрочненных участков использована новая охлаждающая оснастка c экранирующим устройством и жидкий азот в качестве хладагента. Представлены принцип работы и схема экранирующего устройства. Доказано, что при совместном применении теплоотводящей оснастки и экранирующего устройства достигается минимальная ширина зоны разупрочнения. Приведены результаты испытаний цилиндрических образцов в условиях двухосного нагружения при различных значениях параметра двухосности. По данным испытаний определены допустимые размеры зон разупрочнения, при которых несущая способность сварных соединений, ослабленных разупрочненными прослойками, находится на уровне прочности основного упрочненного металла. Доказана эффективность применения предложенной теплоотводяшей оснастки и экранирующей насадки для обеспечения равнопрочности сварных соединений основному металлу изделия. Полученные результаты могут быть использованы на стадии конструктивно-технологического проектирования и изготовления оболочковых изделий из нагартованных алюминиевых сплавов.
Бесплатно
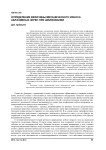
Определение величины механического износа абразивных зерен при шлифовании
Статья научная
Среди различных механизмов износа абразивного инструмента при шлифовании преобладающим является механический, проявляющийся в виде удаления элементарных микрообъемов абразивного материала с рабочей поверхности зерен. Природа образования площадки затупления на зерне в результате данного вида износа до сих пор не раскрыта. В статье предлагается кинетический подход к механическому изнашиванию абразивных зерен при шлифовании на основе термофлуктуационной природы разрушения твердых тел. Полагается, что в результате многократного квазипериодического контакта с обрабатываемым материалом в материале абразивного зерна на межатомных связях возникают перенапряжения, которые служат толчком для преодоления атомами энергетического барьера и разрыва единичной связи. В результате, в абразивном материале происходит накопление разорванных межатомных связей, образуются несплошности и развивается процесс разрушения. При этом немаловажную роль играет температура в зоне обработки. Предложенная методика имитационного моделирования контактного взаимодействия абразивного зерна с материалом позволяет определить напряжения, действующие в зерне при шлифовании и величину долговечности абразивного материала. Установлена характерная зависимость напряжения и долговечности от размера площадки затупления, имеющейся на абразивном зерне. Переход от элементарных объемов абразивного материала, испытывающих напряжения, к макрообъемам позволяет определить величину абразивного материала, изношенного в результате механического взаимодействия с обрабатываемым материалом. Методика прогнозирования величины износа абразивного зерна при эксплуатации шлифовальных кругов различных характеристик в широком диапазоне технологических условий позволит создать совершенно иной подход к проектированию операций абразивной обработки - когда инструмент с определенным ресурсом работоспособности является исходным данным и задача технолога состоит в его эффективной эксплуатации.
Бесплатно
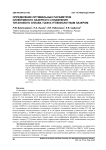
Статья научная
Один из наиболее часто применяемых сплавов в аддитивных технологиях - титановый сплав TiAl6V4. В последние годы большое количество работ посвящалось исследованию селективного лазерного сплавления данного сплава при использовании оптоволоконного лазера. В данной работе исследовались режимы SLM с применением углекислотного лазера. Для исследования влияния параметров селективного лазерного сплавления на пористость получаемого материала использовалась установка SINTERSTATION® Pro DM125 SLM System. Образцы выращивались в инертной атмосфере (содержание кислорода в рабочей камере составляло 500 ppm). В работе использовался порошок титанового сплава с размером частиц от 20 мкм до 63 мкм, средним размером частиц - 44 мкм, средней сферичностью по параметру ISO Roundness - 63,74 %. С использованием девяти различных режимов сплавления были изготовлены образцы кубической формы. Пористость определялась методом исследования шлифа на оптическом микроскопе (изготавливались 2 шлифа: совпадающий с направлением выращивания образца и перпендикулярный направлению выращивания). Все полученные образцы имеют плотную структуру и удовлетворительное качество поверхности. Наибольшую пористость (22,6 %) имеет образец, для сплавления которого использовалась мощность лазера - 100 Вт, время выдержки лазера в координате - 50 мкс (поры в данном случае имеют неправильную форму и большой размер). Наименьшую пористость (0,5 %) имеет образец, для сплавления которого использовалась мощность лазера - 200 Вт, время выдержки лазера в координате - 150 мкс (поры в данном случае имеют сферическую форму и меньшие размеры).
Бесплатно
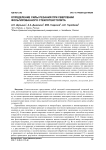
Определение силы резания при сверлении фольгированного стеклотекстолита
Статья научная
В статье приведены результаты экспериментального исследования силы резания при получении отверстий различного диаметра сверлением в слоистом композиционном материале - фольгированном стеклотекстолите. Неоднородная структура материала имеет ограничения по механической обработке, связанные с появлением расслоений из-за неравномерного распределения механической нагрузки. Знания о величине механической нагрузки позволят спрогнозировать наиболее оптимальные режимы резания. В ходе проведения экспериментов получены зависимости изменения осевой составляющей силы резания от подачи при разных частотах вращения, обрабатываемых марках материала и диаметров сверел. В качестве обрабатываемого материала выбраны 3 наиболее распространенные в производстве марки: Isola DE 104, GEM (ILM), СФ2-35 ГОСТ10316-78. Выведена общая закономерность по выбору оптимальных режимов резания при сверлении слоистого композиционного материала. Для оценки влияния затупления режущего инструмента на параметры осевого усилия проведен эксперимент с использованием затупленных сверл диаметром 1 мм на всех трех типах материала по всем ранее выбранным режимам резания. Результат обработки экспериментальных данных показал, что зависимости осевой силы от подачи при использовании обрабатывающего инструмента разного диаметра и разных типов материалов (эпоксидная связка между слоями, стеклоткань, распределение филаментов волокна, разная стеклонаполненность) при одной и той же частоте вращения шпинделя схожи. Полученные зависимости и закономерности позволят построить силовую модель сверления композиционных материалов, что значительно упростит процедуру проектирования операции.
Бесплатно
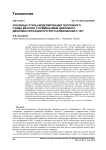
Статья научная
Современные круглошлифовальные станки с ЧПУ позволяют вести обработку по заданным циклам режимов резания, которые являются частью управляющей программы (УП). Несмотря на использование точных систем позирования, современные шлифовальные станки обладают податливостью технологической системы (ТС). Это объясняет колебания величины снимаемого припуска и возникновение различного рода погрешностей размеров, которые увеличиваются при обработке партии деталей, производимой в нестабильных условиях при действии большого количества переменных технологических факторов (колебания припуска, затупления зерен круга, изменения диаметра круга и др.). Однако при наличии большого числа автоматизированных систем проектирования УП до сих пор отсутствует инструмент их контроля на обеспечение точности обработки партии деталей. К тому же при проектировании циклов режимов резания в данных системах используются базы данных, полученные для универсальных станков. В результате проектируемые циклы не гарантируют стабильность показателей точности при обработке партии детали, не обеспечивают максимальную производительность и требуют адаптации к заданным условиям обработки. В данной статье представлено описание цифрового двойника (ЦД) на примере врезного круглого шлифования, который позволяет проводить симуляцию послойного съема металла на протяжении всего цикла шлифования путем расчета величины снимаемого припуска на каждом обороте заготовки при различных сочетаниях нестабильных условий обработки и переменной податливости технологической системы. При этом моделирование послойного удаления припуска осуществляется в нескольких сечениях, которые имеют различную податливость. После окончания моделирования съема металла (в конце цикла шлифования) становится возможным осуществить оценку точности по известным расчетным значениям радиусов во всех сечениях обрабатываемой поверхности. Отметим, что применение ЦД позволит ускорить и упростить процесс проектирования циклов, а также повысить производительность операций круглого шлифования с ЧПУ за счет оптимизации циклов режимов резания с обеспечением заданной точности.
Бесплатно
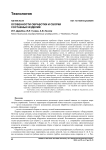
Особенности обработки и сборки составных изделий
Статья научная
В статье рассматриваются проблемы сборки изделий цилиндрической формы, состоящих из секторных деталей имеющих двугранные углы. Одной из основных проблем сборки таких деталей является точность выполнения значений двугранных углов при обработке. На примере сборки изделия из 3-х секторных деталей показано, что даже при точном равенстве двугранных углов 120° не существует однозначности базирования этих деталей при сборке. Поскольку при обработке плоскостей секторных деталей возникают пространственные погрешности двугранных углов, то добиться плотности прилегания плоскостей при сборке практически невозможно. Показаны возможные варианты сборки секторов с суммарным углом больше и меньше 360°. При этом между плоскостями двугранных углов всегда возникает зазор в соединении. Если суммарный угол превысит 360°, сборку осуществить не удается вообще, т.к. невозможно обеспечить прилегание плоскостей двугранного угла. А если суммарный угол окажется меньше 360°, сборку осуществить удается, но при этом появляется заметный угол закрутки или «пропеллерность» секторов в сборе, а также неоднозначность сборки перед обработкой и после обработки. Применив методы аналитической геометрии, мы доказали, что для собираемости без зазора 3-х секторов необходимо и достаточно, чтобы сумма всех двугранных углов секторов была меньше или равна 360°. Поскольку точное равенство суммы всех двугранных углов 360° обеспечить невозможно, то при сборке всегда образуется характерная «пропеллерность». Для получения беззазорного соединения предложен новый метод для селективной сборки секторов и разработана схема приспособления для контроля двугранных углов. Данный метод селективной сборки позволит подбирать секторы таким образом, чтобы угол «закрутки» их в собранном виде был минимальным. При этом можно при подборе секторов устанавливать направление «закрутки» - по часовой или против часовой стрелки, в зависимости от направления сил резания.
Бесплатно
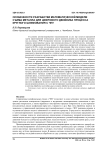
Статья научная
В условиях автоматизированного машиностроения до сих пор остается нерешенной задача проектирования оптимальных циклов режимов резания для операций, выполняемых на станках с ЧПУ. На практике технологу по-прежнему приходится вручную корректировать проектируемые циклы при помощи различных CAD/CAM-систем, имеющих в качестве информационной базы данные из нормативно-справочной литературы, разработанной в 60-90-х годах для универсального оборудования. При этом технолог может опираться только на собственный опыт или же на имеющиеся по аналогичным операциям данные. В результате проектируемые таким образом циклы не могут гарантировать максимальность производительности и стойкость используемого оборудования, стабильность показателей точности и качества в партии деталей, а соответственно, и минимальность себестоимости выполняемой операции. В качестве решения описанной выше проблемы предложена разработка цифрового двойника на примере операции круглого шлифования. Цифровым двойником процесса круглого шлифования может являться аналитическая модель послойного удаления металла с заготовки. Данная модель, помимо исходных условий обработки (основные параметры заготовки, инструмента, оборудования, оснастки и др.), оказывающих непосредственное влияние на процесс шлифования, должна учитывать кинематику и особенности съема металла, присущие различным видам шлифования. Цифровой двойник должен учитывать нестабильность процесса шлифования (затупление круга, колебания припуска, потеря диаметра круга, а соответственно, и площади контакта круга с заготовкой). В статье описаны основные этапы разработки аналитической модели съема металла на примере круглого шлифования с продольной подачей. Разработанный цифровой двойник операции круглого шлифования возможно применять не только при проектировании оптимальных циклов режимов резания, но и для прогнозирования надежности разрабатываемых циклов и качества обработки в нестабильных условиях обработки партии деталей.
Бесплатно

Отработка технологии сварки трением с перемешиванием для соединения труб из алюминиевых сплавов
Статья научная
С целью соединения труб из алюминиевых сплавов проведены исследования технологии сварки трением с перемешиванием: отработаны конструкции инструментов, условия крепления заготовок и режимные параметры. Достигнуто удовлетворительное качество сварного шва.
Бесплатно

Оценка деформаций тонкостенных труб из коррозионностойких сталей при холодной гибке с раскатыванием
Статья научная
Тонкостенные трубы из коррозионностойких сталей находят широкое применение в авиации, ракетостроении, космической технике, судостроении, машиностроении, черной и цветной металлургии, атомной энергетике, химической, нефтяной и газовой промышленности и других отраслях. Гибка труб является одной из основных операций технологического процесса изготовления деталей трубопроводов. Несмотря на это, в современных производственных условиях практически невозможно осуществить качественную гибку в холодном состоянии труб диаметром свыше 60-70 мм, поскольку она сопровождается нежелательными для последующей эксплуатации явлениями: утонением стенки на внешней части трубы, овализацией (сплющивание) поперечного сечения, образованием гофр и изломов на внутренней части. Разработанная в ЮУрГУ технология гибки тонкостенных труб с раскатыванием устраняет перечисленные недостатки. При вращении раскатника, заведённого в трубу с достаточно большим натягом, в каждой точке кольцевой зоны раскатывания возникает знакопеременный изгиб, при котором изгибные напряжения кратковременно достигают предела текучести. В результате при приложении относительно небольшого изгибающего усилия происходит гибка в перемещающейся кольцевой зоне раскатывания. В статье рассмотрены результаты экспериментальной оценки деформаций тонкостенных труб при гибке с раскатыванием. Приведена методика проведения эксперимента. Для проведения экспериментов использовался специальный станок для холодной гибки труб с раскатыванием. В основе способа оценки деформаций был использован «Метод сеток». Были определены величины удлинения и уменьшения длины стенок трубы, участвовавших в гибе. В результате проведенного исследования удалось оценить степень и характер деформации в продольном и поперечном сечении стенок трубы при гибке с раскатыванием и, как следствие, рассчитать указанные деформации и утонения стенок трубы, что является важной эксплуатационной характеристикой.
Бесплатно
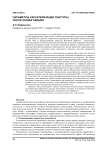
Параметры характеризации текстуры после хонингования
Статья научная
Ресурс агрегатов зависит от условий работы узлов, состоящих из взаимодействующих деталей, формирующих пары трения. Условия контактирования определяются параметрами шероховатости трущихся поверхностей, формируемых финишной механической обработкой. Один из распространённых процессов финишной обработки - хонингование. В конструкторско-технологической документации при назначении операций хонингования нормируются параметры макро- (возможно исправление формы) и микрогеометрии. Традиционно обозначаемая термином «шероховатость» группа параметров, характеризующих микрогеометрию, в настоящее время определяется термином «текстура» поверхности в современных стандартах. Модернизация производства с использованием концепции «Индустрия 4.0» обозначена в стратегии научно-технологического развития Российской Федерации как «переход к передовым цифровым, интеллектуальным производственным технологиям». Для области «Технологии машиностроения» данный приоритет обуславливает необходимость в достоверных моделях, отражающих технологические процессы, включая целевые функции и их оценку (формообразование - погрешности формы, шероховатость - параметры шероховатости) каждого из технологических процессов для включения в дальнейшем данных процессов в единую государственную информационную систему контроля за производственными цепочками, разрабатываемую в настоящее время в Министерстве промышленности и торговли Российской Федерации. Экономическая целесообразность развития данного направления связана с ростом вклада государства (госкомпаний) в ВВП с 35 % в 2005 году до 70 % в 2015 году, согласно данным Федеральной антимонопольной службы Российский Федерации. Какие параметры микрогеометрии применяются исследователями для оценки получаемой поверхности после хонингования при проведении экспериментальных исследований и при построении моделей и какие параметры являются приоритетными для машиностроительных предприятий, рассмотрено в данной статье. Приведен обзор публикаций в области хонингования включая анализ нормируемых исследователями параметров текстуры. Рассмотрены основные пути развития хонингования, в части нормирования параметров, получаемых после обработки.
Бесплатно
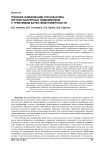
Плоское шлифование торцов колец крупногабаритных подшипников с требуемым качеством поверхности
Статья научная
Кольца подшипников после термообработки приобретают отклонение от плоскостности и изогнутость торцовых поверхностей под действием остаточных температурных напряжений. Наличие изогнутости торцовой поверхности существенно усложняет процесс шлифования, поскольку под действием магнитного поля стола станка кольца получают дополнительную деформацию. Исследуется плоское шлифование периферией круга образцов из стали ШХ15. Математические модели приведённых к ширине образца составляющих силы резания, коэффициента шлифования и шероховатости обработанной поверхности (параметр Ra) получены методом полного факторного эксперимента типа 24, где 4 - число факторов. Экспериментальные исследования проведены при плоском шлифовании периферией круга образцов из стали ШХ15. Представлены алгоритмы и математические модели для определения осевой деформации при шлифовании колец крупногабаритных подшипников с начальными отклонениями от плоскостности торцов. Анализ формы торцовой поверхности нежестких колец сделан на примере наружных колец конического однорядного роликоподшипника из стали ШХ15. Для определения максимальных осевых упругих деформаций при изгибе кольца используется теория стержней малой кривизны. Максимальная осевая упругая деформация кольца при изгибе определяется методом Мора. Статическая неопределимость кольца раскрывается методом сил. Определяются условия обеспечения заданного допуска плоскостности торцовой поверхности кольца подшипника, учитывающие осевую деформацию кольца под действием магнитного поля станка и радиальной составляющей силы резания. Представлены алгоритм и методика определения оптимальных условий шлифования торцовой поверхности колец подшипников, обеспечивающих получение заданных требований к качеству обработанной поверхности (Ra, допуск плоскостности, отсутствие шлифовочных прижогов) при максимальной производительности процесса.
Бесплатно
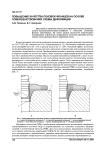
Повышение качества поковок фланцев на основе совершенствования схемы деформации
Статья обзорная
Предложена и опробована новая схема деформации методом прошивка-раздача-выдавливание/вытяжка-калибровка в технологии штамповки фланцев воротниковых. На основе анализа результатов компьютерного моделирования и физических экспериментов установлен критерий качества поковок и рекомендована область применения схемы.
Бесплатно
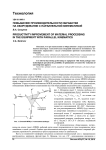
Повышение производительности обработки на оборудовании с параллельной кинематикой
Статья научная
Показано, что при выполнении на оборудовании с параллельными приводами некоторых технологических операций появляется возможность оптимизации управления с целью уменьшения времени выполнения этих операций.
Бесплатно

Повышение производительности точения резьбы резцами с керамическими пластинками
Статья научная
Несмотря на множество хорошо разработанных процессов высокопроизводительного формирования резьб давлением на деталях массового производства в некоторых случаях приходится нарезать резьбы резцами. К таким случаям относят нарезание резьбы на тонкостенных заготовках или повышенной твердости, нарезание резьб несимметричного профиля. Ведущие инструментальные фирмы разрабатывают и выпускают для этих случаев специальные резьбовые пластины и дают программы для расчета режимов резания и схемы срезания припуска в зависимости от шага резьбы и твердости обрабатываемой заготовки. Обычно резьбовые пластины изготавливают из металлокерамических твердых сплавов, зачастую с упрочняющими покрытиями. Особенностью профиля резьбовых пластинок является малый радиус скругления вершины, связанный с размерами шага нарезаемой резьбы. Это обстоятельство приводит к высоким механическим и тепловым нагрузкам на вершину резьбовой пластины и вынуждает для обеспечения приемлемой стойкости снижать режимы резания: скорость, связанную с частотой вращения заготовки, и подачу врезания на каждый рабочий ход. В последнее время появились пластинки из минералокерамики на основе окиси алюминия с легированием карбидами тугоплавких металлов. Эти пластинки обладают высокой теплостойкостью, что позволяет повышать скорость резания. Однако в литературе практически нет сведений о применении пластинок из минералокерамики для нарезания резьбы на высокопрочных заготовках. В статье приведены результаты экспериментов по нарезанию резьбы резцами с керамическими пластинками на стальных заготовках высокой твердости (HRC 52…55). Показано влияние отрицательного переднего угла, величины заглубления резца и подачи на врезание на составляющие силы резания. Доказано, что при оптимизации геометрических параметров пластинок возможно высокопроизводительно нарезать резьбы на закаленных заготовках из высокопрочных материалов, что в сочетании с меньшей стоимостью материала пластинок сулит существенные экономические преимущества.
Бесплатно
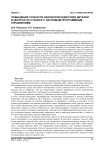
Статья научная
В статье описывается метод расчета траектории движения токарного инструмента на станке с числовым программным управлением для компенсации упругой деформации при обработке заготовки. В процессе точения тел вращения с малой жесткостью под действием режущей силы Py происходят упругие деформации, что негативно влияет на точность обработанной поверхности. Вследствие этого появляется погрешность в виде бочкообразности, седлообразности или комбинации данных погрешностей в зависимости от жесткости станка и его отдельных частей. На основе расчета деформации при постоянной глубине резания предлагается определить погрешность, которую необходимо в дальнейшем компенсировать с помощью приведенного метод расчета. Он позволяет проводить компенсацию за счет предыскажения траектории на этапе программирования управляющей программы. Тем самым в процессе точения будет получен требуемый диаметр с минимальными погрешностями, что в свою очередь положительно будет влиять на сокращение дополнительной обработки для удаления погрешностей формы и повышения качества обработки детали.
Бесплатно
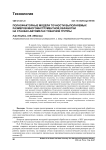
Статья научная
В данной статье показано современное состояние разработки теории проектирования многоинструментной обработки на станках-автоматах токарной группы. Отмечено, что существующие модели погрешности обработки учитывают лишь плоско-параллельные перемещения подсистем технологической системы вдоль координатных осей декартовой системы координат X, Y, Z. Такой подход к моделированию процесса образования погрешностей обработки допустим для деталей, имеющих габаритные размеры одного порядка по всем координатным направлениям. Однако на практике нередки случаи, когда обрабатываются детали с габаритными размерами, существенно различающимися в разных направлениях. В этих случаях существенный вклад в погрешность обработки могут вносить повороты обрабатываемой заготовки, особенно по направлениям преобладающих габаритных размеров. Поэтому указана необходимость учета угловых перемещений заготовки под действием сил резания в этих моделях. С этой целью были разработаны полнофакторная матричная модель искажения и поля рассеяния выполняемых размеров многоинструментной двухсуппортной обработки. В этих моделях учитывается комплексная характеристика податливости технологической системы, то есть, кроме собственных упругих свойств системы (плоско-параллельных перемещений технологических подсистем, их угловых перемещений вокруг базовых точек), еще и параметры наладки, для которой эта податливость рассматривается. Поэтому для формирования комплексной характеристики податливости подсистемы были проведены эксперименты по определению податливостей подсистемы технологической системы. Наличие фактических матричных характеристик податливости для реального станка позволяет оценить практическую применимость разработанных полнофакторных матричных моделей точности обработки. В результате появится возможность выявлять степень влияния на точность обработки комплекса технологических факторов, включая структуру многоинструментной наладки, деформационных свойств подсистем технологической системы, режимов резания.
Бесплатно

Получение металлических микропорошков газодинамическим распылением
Статья научная
Показаны технологические схемы распыления металла с плавлением в тигле и бесконтактным способом. Оценены режимы и характеристики получаемого материала.
Бесплатно